Scouts not allowed to have an allotment
Issue
The enquirer has been advised by the chair of their local allotment community gardens site that a group of scouts under the supervision of a leader can not have a plot, for "health and safety& reasons. The scouts are keen to grow their own veg, and an allotment would be ideal for a small group to get started with.Panel decision
Although there are some minor risks associated with cultivating an allotment (use of tools, possible use of chemicals) these are all easily manageable with proper supervision which one could reasonably expect the Scout movement to provide.The panel strongly believes that this is an excellent opportunity for Scouts to become involved in growing food and getting physical exercise and it is a great pity that "health and safety" has been offered up as a poor excuse for not allowing them to do it. The allotment committee should own up to their true reasons for refusing this worthwhile project.
Family told they must use the indoor play barn before the outdoor activities at a petting farm
Issue
The enquirer visited a mini farm which also had an adventure playground and fishing lakes outside and an indoor soft play barn. They were told that if they wanted to use the indoor play barn they would have to pay and use this first before looking around the outside attractions due to "health and safety" reasons.Panel decision
Young children are particularly vulnerable to zoonotic infections such as E-coli and good hygiene is very important in petting farms. This establishment has decided to implement a rule that the indoor play barn should be used before petting the animals to avoid the risk of any child picking up an infection from contaminated play equipment. In the panel’s view this is an entirely sensible measure, but the staff need to be trained to understand the reasons and be prepared to explain that clearly to visitors.Motorcyclist told to remove helmet and get off the motorcycle whilst refuelling
Issue
The enquirer, whilst refuelling a motorcycle at a filling station, was asked to remove their safety helmet before the pump was switched on. Then on another occasion they were asked to get off the motorcycle before refuelling. The enquirer wrote to the supermarket filling station CEO requesting an explanation and was told this was for ‘Health and Safety’ reasons.Panel decision
Requiring motorcyclists to remove their helmets at filling stations is not a health and safety issue. It appears to be a measure to discourage and prevent fuel theft. This is understandable but the filling station should be clear about the real reason.Requiring motorcyclists and passengers to dismount and place the motorcycle on its stand during refuelling is a sensible measure which is stated in the Energy Institute’s guidance on petrol station refuelling. It enables better control of the refilling operation, reduces the risk of spilling fuel on clothes, high temperature parts of the motorcycle itself and on the forecourt. A clearer explanation by the supermarket of the logic behind both of these requirements would have been helpful.
Apartment balconies not to be used for washing and storage
Issue
The enquirer recently moved into rented accommodation with large (half enclosed balconies), however all residents have been sent a letter saying that balconies should not be used for hanging washing, storing large plants or bicycles due to health and safety.Panel decision
When properties have balconies it is reasonable to assume they are there to be used and it is difficult to understand why a ban on certain uses of the balconies has been put in place. The panel’s view is that this is a mis-use of "health and safety" as an excuse for banning the use of balconies for activities which would detract from the overall appearance of the property. Tenants deserve a proper explanation.National clampdown targets construction industry’s poor health record
- ‘Health as well as safety’ will be the message as poor standards and unsafe work on Britain’s building sites are targeted as part of a nationwide drive aimed at reducing ill health, death and injury in the industry.
During the month long initiative, the Health and Safety Executive (HSE) will carry out unannounced visits to sites where refurbishment projects or repair works are underway.
From 22 September, HSE Inspectors will ensure high-risk activities particularly those affecting the health of workers, are being properly managed. These include working with harmful dusts such as silica and asbestos, and other hazardous substances. If unacceptable standards are found Inspectors will take immediate enforcement action.
HSE is urging industry to ‘think health’ as over 30,000 construction workers are made ill by their work every year.
Philip White, HSE Chief Inspector of Construction, said:
“Industry has made much progress in reducing the number of people killed and injured in its activities, but for every fatal accident, approximately 100 construction workers die from a work-related cancer.
During the recent health initiative, enforcement action was taken on one in six sites. Time and again we find smaller contractors working on refurbishment and repair work failing to protect their workers through a lack of awareness and poor control of risks.
This isn’t acceptable – it costs lives, and we will take strong and robust action where we find poor practice and risky behaviour.
Through campaigns like this we aim to ensure contractors take all risks to their workers seriously, and not just focus on immediate safety implications. They need to put in place practical measures to keep workers both safe and well”
From 22 September, HSE Inspectors will ensure high-risk activities particularly those affecting the health of workers, are being properly managed. These include working with harmful dusts such as silica and asbestos, and other hazardous substances. If unacceptable standards are found Inspectors will take immediate enforcement action.
HSE is urging industry to ‘think health’ as over 30,000 construction workers are made ill by their work every year.
Philip White, HSE Chief Inspector of Construction, said:
“Industry has made much progress in reducing the number of people killed and injured in its activities, but for every fatal accident, approximately 100 construction workers die from a work-related cancer.
During the recent health initiative, enforcement action was taken on one in six sites. Time and again we find smaller contractors working on refurbishment and repair work failing to protect their workers through a lack of awareness and poor control of risks.
This isn’t acceptable – it costs lives, and we will take strong and robust action where we find poor practice and risky behaviour.
Through campaigns like this we aim to ensure contractors take all risks to their workers seriously, and not just focus on immediate safety implications. They need to put in place practical measures to keep workers both safe and well”
Construction firm sentenced after barrier fell on baby’s pram
- A construction firm has been fined for safety failings after a barrier was blown on top of a pram injuring an 18-week-old baby.
The baby boy was asleep in his pram while his mother used a cash machine outside a supermarket in Drip Road, Stirling, when the incident occurred on 24 October 2011.
Stirling Sheriff Court was told that Kier Construction Ltd was refurbishing the supermarket and had assembled barriers to separate the public from the work that was going on. Branding banners saying the supermarket was still open for business were attached to the barriers.
The court heard the baby’s mother parked the pram near to the barriers with her 13-year-old daughter, standing next to it. As she walked to the cash machine she heard her daughter scream. She turned and saw a barrier with banner attached had fallen on top of the pram hood, which had collapsed on the baby. They tried to lift the barrier off the pram and a passer-by came to their assistance.
The baby was taken to hospital with bruising to his forehead. He was discharged that day and suffered no more effects from the incident.
An investigation by the HSE found that contrary to manufacturer’s instructions, the barriers had not been filled with water to ensure stability and the barriers next to the cash machines had not been locked together.
Inspectors also discovered that the previous month, high winds had caused the barriers to fall over and the site manger had ordered the removal of the banners. Concrete blocks were then placed at the base of the barriers but they were not filled with water.
Kier Construction Ltd, of, Tempsford Hall, Sandy, Bedfordshire, was fined £4,000 after pleading guilty to breaching Section 3 of the Health and Safety at Work etc Act 1974.
Following the case, HSE Principal Inspector Isabelle Martin, said:
“This incident could easily have been prevented. If assembled correctly the barriers could withstand winds of up to 58mph. On the day of the incident windspeed was about 30mph and should not have been an issue.
“Instead, because Kier Construction Limited failed to properly construct the barriers, a young baby was hurt. Luckily, his injuries were minor but they could have been worse. This incident should serve as a reminder to construction companies about their duty to protect members of the public who may be affected by their work.”
Stirling Sheriff Court was told that Kier Construction Ltd was refurbishing the supermarket and had assembled barriers to separate the public from the work that was going on. Branding banners saying the supermarket was still open for business were attached to the barriers.
The court heard the baby’s mother parked the pram near to the barriers with her 13-year-old daughter, standing next to it. As she walked to the cash machine she heard her daughter scream. She turned and saw a barrier with banner attached had fallen on top of the pram hood, which had collapsed on the baby. They tried to lift the barrier off the pram and a passer-by came to their assistance.
The baby was taken to hospital with bruising to his forehead. He was discharged that day and suffered no more effects from the incident.
An investigation by the HSE found that contrary to manufacturer’s instructions, the barriers had not been filled with water to ensure stability and the barriers next to the cash machines had not been locked together.
Inspectors also discovered that the previous month, high winds had caused the barriers to fall over and the site manger had ordered the removal of the banners. Concrete blocks were then placed at the base of the barriers but they were not filled with water.
Kier Construction Ltd, of, Tempsford Hall, Sandy, Bedfordshire, was fined £4,000 after pleading guilty to breaching Section 3 of the Health and Safety at Work etc Act 1974.
Following the case, HSE Principal Inspector Isabelle Martin, said:
“This incident could easily have been prevented. If assembled correctly the barriers could withstand winds of up to 58mph. On the day of the incident windspeed was about 30mph and should not have been an issue.
“Instead, because Kier Construction Limited failed to properly construct the barriers, a young baby was hurt. Luckily, his injuries were minor but they could have been worse. This incident should serve as a reminder to construction companies about their duty to protect members of the public who may be affected by their work.”
Builder photographed risking lives
- A Wirral builder was caught on camera risking the lives of his workers on a house roof, a court has heard.
Ronald Steven King, known as Steve, and two other men were seen on the roof of a detached house in Kingsley, Cheshire, without any measures in place to prevent them being injured in a fall.
An inspector from the HSE, who visited the site following a complaint by a member of the public, also found the workers had to jump over a one-metre gap from a scaffolding tower to reach the roof.
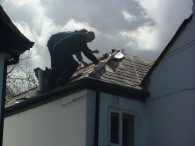
Steve King and another worker on a house roof in Kingsley
Mr King was prosecuted by HSE following the inspection of the work on the four-bedroomed house on Brookside on 29 April 2013.
Chester Magistrates’ Court heard that the 61-year-old had been hired to re-roof the property, including replacing slates and fitting insulation, and had begun work on the project two weeks earlier.
A scaffolding tower had been erected in a neighbouring garden but there was a large gap from the scaffolding to the house roof. There were also no scaffolding boards or other protection around the edge of the roof to prevent workers falling up to four and a half metres.
Mr King, of Airlie Road in Hoylake, was fined £3,000 and ordered to pay £2,457 in prosecution costs on 25 September 2014 after pleading guilty to a breach of the Work at Height Regulations 2005 by failing to put measures in place to prevent falls.
Speaking after the hearing, HSE Inspector Kevin Jones said: “Mr King is an experienced roofer and had taken on a major project to re-roof a detached house but he failed to make sure basic safety measures were in place.
“He not only put his own life at risk but also the lives of two of the workers he employed by asking them to jump from the scaffolding to the roof, and by not providing protection around the edge of the roof.
“The risks from working at height are well known in the construction industry but Mr King ignored the dangers. If we hadn’t been alerted to the work by a member of the public, then I dread to think what might have happened.”
An inspector from the HSE, who visited the site following a complaint by a member of the public, also found the workers had to jump over a one-metre gap from a scaffolding tower to reach the roof.
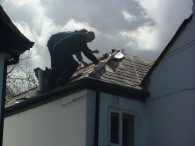
Steve King and another worker on a house roof in Kingsley
Mr King was prosecuted by HSE following the inspection of the work on the four-bedroomed house on Brookside on 29 April 2013.
Chester Magistrates’ Court heard that the 61-year-old had been hired to re-roof the property, including replacing slates and fitting insulation, and had begun work on the project two weeks earlier.
A scaffolding tower had been erected in a neighbouring garden but there was a large gap from the scaffolding to the house roof. There were also no scaffolding boards or other protection around the edge of the roof to prevent workers falling up to four and a half metres.
Mr King, of Airlie Road in Hoylake, was fined £3,000 and ordered to pay £2,457 in prosecution costs on 25 September 2014 after pleading guilty to a breach of the Work at Height Regulations 2005 by failing to put measures in place to prevent falls.
Speaking after the hearing, HSE Inspector Kevin Jones said: “Mr King is an experienced roofer and had taken on a major project to re-roof a detached house but he failed to make sure basic safety measures were in place.
“He not only put his own life at risk but also the lives of two of the workers he employed by asking them to jump from the scaffolding to the roof, and by not providing protection around the edge of the roof.
“The risks from working at height are well known in the construction industry but Mr King ignored the dangers. If we hadn’t been alerted to the work by a member of the public, then I dread to think what might have happened.”
Residents’ lives put at risk by gas faults in 349 properties
- A plumbing and heating company, and two self-employed people who worked for them, have been sentenced following an investigation into a significant number of faulty gas installations at new developments in Poole and Reading.
The investigation by the HSE led to the prosecution of DSI Plumbing and Heating, Robert Percival and Andrew Church, at Bournemouth Crown Court.
The court heard that Harbour Reach in Poole contained 261 flats and 79 town houses, while Caversham Road in Reading contained 60 flats. These were heated by gas boilers installed on internal walls, with flue gases, including poisonous carbon monoxide, vented to the open air by flues installed in building voids. In such situations inspection hatches must be provided to allow the flues to be periodically checked for safety.
At Harbour Reach, HSE’s investigations found faults including gas leaks, and flues and gas supply pipes that had not been properly fitted – establishing that the initial installation work was substandard, and that the final checking and commissioning of the work was inadequate and ineffective.
There were no inspection hatches originally installed in any of the ceilings of the flats, meaning that the flues could not be subsequently checked for safety. As a result, the gas supply to all 340 gas meters on the Harbour Reach site had to be disconnected until remedial action was taken.
The investigation also revealed evidence of defects in the installations in 309 (or over 90%) of the dwellings at Harbour Reach. At Caversham Road in Reading, HSE’s investigation uncovered defects in the gas installation affecting 40 properties. As at Harbour Reach, inspection hatches were not initially installed to allow the flue system to be inspected, and defects were found with both gas supply and flue installations.
Mr Church completed the commissioning documents for the work without carrying out the required checks.
DSI Plumbing and Heating Ltd, of The Square, Fawley, near Southampton pleaded guilty to two breaches of the Health and Safety at Work Act 1974 and was fined a total of £10,000 and ordered to pay a further £1,000 in costs.
Robert Percival, of Legion Road, Poole, and Andrew Church, of Ensign Drive, Gosport, both pleaded guilty to a single breach of the same legislation, Mr Percival for his commissioning of gas installations at one property, and Mr Church for making false entries into documents. They were both given a two year conditional discharge and were each ordered to pay costs of £250.
After sentencing, HSE Head of Operations, Harvey Wild, said:
“These serious failings involving gas safety only came to light after residents started to complain about ill-health. It is fortunate that in this case, no-one suffered long term ill-effects but the consequences of the faults, if left undetected, could have been fatal.
“Gas installers need to make sure flues and pipes can be properly checked and all installations are checked for safety as part of commissioning to ensure lives are not put at risk.”
The court heard that Harbour Reach in Poole contained 261 flats and 79 town houses, while Caversham Road in Reading contained 60 flats. These were heated by gas boilers installed on internal walls, with flue gases, including poisonous carbon monoxide, vented to the open air by flues installed in building voids. In such situations inspection hatches must be provided to allow the flues to be periodically checked for safety.
At Harbour Reach, HSE’s investigations found faults including gas leaks, and flues and gas supply pipes that had not been properly fitted – establishing that the initial installation work was substandard, and that the final checking and commissioning of the work was inadequate and ineffective.
There were no inspection hatches originally installed in any of the ceilings of the flats, meaning that the flues could not be subsequently checked for safety. As a result, the gas supply to all 340 gas meters on the Harbour Reach site had to be disconnected until remedial action was taken.
The investigation also revealed evidence of defects in the installations in 309 (or over 90%) of the dwellings at Harbour Reach. At Caversham Road in Reading, HSE’s investigation uncovered defects in the gas installation affecting 40 properties. As at Harbour Reach, inspection hatches were not initially installed to allow the flue system to be inspected, and defects were found with both gas supply and flue installations.
Mr Church completed the commissioning documents for the work without carrying out the required checks.
DSI Plumbing and Heating Ltd, of The Square, Fawley, near Southampton pleaded guilty to two breaches of the Health and Safety at Work Act 1974 and was fined a total of £10,000 and ordered to pay a further £1,000 in costs.
Robert Percival, of Legion Road, Poole, and Andrew Church, of Ensign Drive, Gosport, both pleaded guilty to a single breach of the same legislation, Mr Percival for his commissioning of gas installations at one property, and Mr Church for making false entries into documents. They were both given a two year conditional discharge and were each ordered to pay costs of £250.
After sentencing, HSE Head of Operations, Harvey Wild, said:
“These serious failings involving gas safety only came to light after residents started to complain about ill-health. It is fortunate that in this case, no-one suffered long term ill-effects but the consequences of the faults, if left undetected, could have been fatal.
“Gas installers need to make sure flues and pipes can be properly checked and all installations are checked for safety as part of commissioning to ensure lives are not put at risk.”
Home improvement company fined for potentially lethal work
- Two partners in a home improvement company have been fined after building work at a house exposed a woman and her foster children to the risk of carbon monoxide poisoning.
The company, run by Janusz Wojcik and Phillip Thomas, was contracted to carry out loft conversion work at a property in Bettws, near Newport, on behalf of Newport City Council in November 2010.
As part of the improvement work the company had to replace a flue from the gas fire, which they left in an ‘immediately dangerous’ condition with the potentially lethal fumes escaping into the loft space.
In a prosecution brought by the Health and Safety Executive (HSE), Cardiff Crown Court heard that the householder had agreed to modifications to her home with a grant from the council to accommodate foster children.
The householder, who lives at her home with four adolescents, had concerns about the quality of the work carried out by the company, and found that there were faults with the plumbing system. Gas Safe Register, who sent an officer to investigate, found that the flue from the gas fire had been removed from just below the level of the loft, allowing poisonous carbon monoxide gas into the loft space. It was classified as ‘immediately dangerous’.
HSE’s investigation identified that the partnership did not obtain advice from a Gas Safe registered engineer before the chimney and flue were removed. The gas fire was still connected and used during the winter resulting in potentially deadly carbon monoxide gas building-up in the loft space.
Janusz Wojcik, and Phillip Thomas, partners of P Thomas and J Building and Home Improvement Specialists of Lochaber Street, Cardiff, each pleaded guilty to a breach of the Gas Safety (Installation and Use) Regulations. Both defendants were fined £1,500 each.
HSE Inspector Dean Baker, speaking after the hearing, said: “Janusz Wojcik and Phillip Thomas failed in their duty to ensure the gas fire was made safe before they removed the chimney and flue.
“The shoddy and careless work by the contractors could have cost a family with young children their lives. Anyone carrying out work on or near a flue should get the advice of a Gas Safe Registered engineer before starting work to ensure it is made safe. It is never acceptable to assume that a gas appliance will not be used after a flue has been removed”.
The householder, who does not want to be named, said: “The council approached me with a view to having a loft conversion to help with fostering. The contractors they chose for the job were not competent and put me and my foster children at risk.
“My son started complaining of headaches and feeling sick and I put it down to him playing computer games, not carbon monoxide. When the Gas Safe Register Inspector found that the flue had been removed I realised just how lucky we were.”
As part of the improvement work the company had to replace a flue from the gas fire, which they left in an ‘immediately dangerous’ condition with the potentially lethal fumes escaping into the loft space.
In a prosecution brought by the Health and Safety Executive (HSE), Cardiff Crown Court heard that the householder had agreed to modifications to her home with a grant from the council to accommodate foster children.
The householder, who lives at her home with four adolescents, had concerns about the quality of the work carried out by the company, and found that there were faults with the plumbing system. Gas Safe Register, who sent an officer to investigate, found that the flue from the gas fire had been removed from just below the level of the loft, allowing poisonous carbon monoxide gas into the loft space. It was classified as ‘immediately dangerous’.
HSE’s investigation identified that the partnership did not obtain advice from a Gas Safe registered engineer before the chimney and flue were removed. The gas fire was still connected and used during the winter resulting in potentially deadly carbon monoxide gas building-up in the loft space.
Janusz Wojcik, and Phillip Thomas, partners of P Thomas and J Building and Home Improvement Specialists of Lochaber Street, Cardiff, each pleaded guilty to a breach of the Gas Safety (Installation and Use) Regulations. Both defendants were fined £1,500 each.
HSE Inspector Dean Baker, speaking after the hearing, said: “Janusz Wojcik and Phillip Thomas failed in their duty to ensure the gas fire was made safe before they removed the chimney and flue.
“The shoddy and careless work by the contractors could have cost a family with young children their lives. Anyone carrying out work on or near a flue should get the advice of a Gas Safe Registered engineer before starting work to ensure it is made safe. It is never acceptable to assume that a gas appliance will not be used after a flue has been removed”.
The householder, who does not want to be named, said: “The council approached me with a view to having a loft conversion to help with fostering. The contractors they chose for the job were not competent and put me and my foster children at risk.
“My son started complaining of headaches and feeling sick and I put it down to him playing computer games, not carbon monoxide. When the Gas Safe Register Inspector found that the flue had been removed I realised just how lucky we were.”
Salford recycling firm sentenced over worker’s crushed leg
- A recycling firm has appeared in court after an employee almost lost his right leg when it became trapped in a machine at a Swinton factory.
Nearly a year after the incident, doctors still do not know whether the 41-year-old from Middleton, who has asked not to be named, will ever regain the full use of his leg.
Roydon Polythene (Exports) Ltd was prosecuted by the HSE after an investigation found workers at the plant at Junction Eco Park were routinely put at risk when they tried to remove blockages.
Trafford Magistrates’ Court heard that the employee had been trying to clear a jam in a glass sorting machine on 16 October 2013.
He was lifted in a mobile elevating work platform, similar in appearance to a cherry picker, before climbing out of the basket and onto a conveyor belt, more than four metres above the ground. As he tried to clear the blockage, his right leg was drawn into the machinery.
His leg remained trapped for more than two hours while emergency services tried to cut him free. He sustained significant crush injuries, requiring multiple operations to try and save his leg.
The court was told that it had become routine for workers to climb from the lifting basket onto the conveyor belt to clear blockages from an unguarded part of the machine. There were also no guard rails around the edge of the conveyor to prevent employees from falling to the ground below.
Roydon Polythene (Exports) Ltd, of Rake Lane in Swinton, was fined £10,000 and ordered to pay £1,221 in prosecution costs after pleading guilty to single breaches of the Provision and Use of Work Equipment Regulations 1998 and the Work at Height Regulations 2005.
The charges relate to failing to prevent access to dangerous parts of machinery, and failing to put measures in place to prevent workers falling from height.
Speaking after the hearing, HSE Inspector Jackie Worrall said: “A worker has suffered severe injuries that will affect him for the rest of his life because his employer failed in its duty to ensure he stayed safe at work.
“This wasn’t a one-off incident. Instead, workers were routinely expected to climb onto the conveyor belt to clear blockages from an unguarded part of the machine, putting their lives at risk. It was therefore almost inevitable that someone would be injured, either by becoming trapped in the machine or falling to the ground below.
“Roydon Polythene should have carried out a proper assessment of the risks facing its employees, and taken action to put safety measures in place. If it had then the worker’s injuries could have been avoided.”
Roydon Polythene (Exports) Ltd was prosecuted by the HSE after an investigation found workers at the plant at Junction Eco Park were routinely put at risk when they tried to remove blockages.
Trafford Magistrates’ Court heard that the employee had been trying to clear a jam in a glass sorting machine on 16 October 2013.
He was lifted in a mobile elevating work platform, similar in appearance to a cherry picker, before climbing out of the basket and onto a conveyor belt, more than four metres above the ground. As he tried to clear the blockage, his right leg was drawn into the machinery.
His leg remained trapped for more than two hours while emergency services tried to cut him free. He sustained significant crush injuries, requiring multiple operations to try and save his leg.
The court was told that it had become routine for workers to climb from the lifting basket onto the conveyor belt to clear blockages from an unguarded part of the machine. There were also no guard rails around the edge of the conveyor to prevent employees from falling to the ground below.
Roydon Polythene (Exports) Ltd, of Rake Lane in Swinton, was fined £10,000 and ordered to pay £1,221 in prosecution costs after pleading guilty to single breaches of the Provision and Use of Work Equipment Regulations 1998 and the Work at Height Regulations 2005.
The charges relate to failing to prevent access to dangerous parts of machinery, and failing to put measures in place to prevent workers falling from height.
Speaking after the hearing, HSE Inspector Jackie Worrall said: “A worker has suffered severe injuries that will affect him for the rest of his life because his employer failed in its duty to ensure he stayed safe at work.
“This wasn’t a one-off incident. Instead, workers were routinely expected to climb onto the conveyor belt to clear blockages from an unguarded part of the machine, putting their lives at risk. It was therefore almost inevitable that someone would be injured, either by becoming trapped in the machine or falling to the ground below.
“Roydon Polythene should have carried out a proper assessment of the risks facing its employees, and taken action to put safety measures in place. If it had then the worker’s injuries could have been avoided.”
Basingstoke company in court after worker crushed
- A Basingstoke engineering firm has been sentenced for safety breaches that led to a 42-year-old man being crushed between a telehandler and a steel post at a workshop in West Drayton.
The man, from Berkshire, suffered life-threatening injuries when he was trapped by the machine against the post as he acted as a lookout for the vehicle.
He had to have his spleen and most of his pancreas removed and was in hospital for four months after the incident. He has yet to be able to return to work, but is hoping to do so shortly.
The incident, on 25 September 2013, was investigated by the HSE, which prosecuted RVC Engineering Ltd for safety failings at Westminster Magistrates’ Court.
The court was told that an impromptu operation had been taking place to enable workers to shunt a broken-down telehandler into the RVC workshop. It was agreed that an HGV would be reversed up to the vehicle to push it just the few feet it needed to end up within the unit.
The injured person was asked to act as a lookout but became trapped between the moving telehandler and the post. He was freed within a few minutes but had suffered severe crush injuries.
RVC Engineering Ltd, of Springpark House, Basing View, Basingstoke, Hants, was fined £6,600 and ordered to pay £1,087 in costs after admitting a breach of Section 2(1) of the Health and Safety at Work etc Act 1974.
After the hearing, HSE Inspector Pete Collingwood said:
“A worker suffered a very serious injury from what was perceived to be an innocuous operation. It was an entirely preventable injury as the maneovre could have been conducted without the need for his involvement.
“Crush injuries are common from reversing vehicles in industry. RVC Engineering should have planned this operation carefully despite it being of a short duration and then ensured the whole thing was adequately supervised.”
He had to have his spleen and most of his pancreas removed and was in hospital for four months after the incident. He has yet to be able to return to work, but is hoping to do so shortly.
The incident, on 25 September 2013, was investigated by the HSE, which prosecuted RVC Engineering Ltd for safety failings at Westminster Magistrates’ Court.
The court was told that an impromptu operation had been taking place to enable workers to shunt a broken-down telehandler into the RVC workshop. It was agreed that an HGV would be reversed up to the vehicle to push it just the few feet it needed to end up within the unit.
The injured person was asked to act as a lookout but became trapped between the moving telehandler and the post. He was freed within a few minutes but had suffered severe crush injuries.
RVC Engineering Ltd, of Springpark House, Basing View, Basingstoke, Hants, was fined £6,600 and ordered to pay £1,087 in costs after admitting a breach of Section 2(1) of the Health and Safety at Work etc Act 1974.
After the hearing, HSE Inspector Pete Collingwood said:
“A worker suffered a very serious injury from what was perceived to be an innocuous operation. It was an entirely preventable injury as the maneovre could have been conducted without the need for his involvement.
“Crush injuries are common from reversing vehicles in industry. RVC Engineering should have planned this operation carefully despite it being of a short duration and then ensured the whole thing was adequately supervised.”
Company prosecuted after worker suffers back injury in fork lift fall
- A fork lift truck company has been fined after a worker at its West Bromwich factory fractured a vertebra in his back when one of its vehicles fell from a lorry.
Black Country Magistrates’ Court heard that 58-year-old Terence Jones was unloading the forklift at Linde Creighton Ltd, in Dartmouth Road, by driving it down a ramp.
However, the ramp dislodged from the trailer, causing it and the forklift to drop straight down. The truck fell around 1.2 metres, landing upright on all four wheels in the incident on 21 October 2013.
An investigation by the HSE found the ramp had not been securely attached to the trailer using both the chains it came with. Although one of the two chains had been attached, the other was left off as overhanging bushes made it difficult to get to the far side of the ramp.
The investigation also found the company had failed to risk assess the activity and monitor and enforce the safe system of work to ensure staff used all the safety critical features when attaching the ramp.
Linde Creighton Ltd, of Kingsclere Road, Basingstoke, was fined £8,000 and ordered to pay £1,144 in costs after pleading guilty to breaching Section 2(1) of the Health and Safety at Work etc Act 1974.
After the hearing, HSE inspector Caroline Lane said:
“Mr Jones had used the ramp at least twice a day to unload fork lift truck deliveries since the company bought it in 2008. The ramp manufacturer had provided instructions for its use, and safety warnings and precautions in the operating and maintenance manual clearly stated that unless restrained, the ramp could move away from the dock of the vehicle and that personnel could fall.
“The incident was therefore entirely foreseeable and preventable. Linde Creighton Ltd had a clear, easily achievable standard to meet but failed to achieve it, resulting in a painful injury to a member of staff.”
However, the ramp dislodged from the trailer, causing it and the forklift to drop straight down. The truck fell around 1.2 metres, landing upright on all four wheels in the incident on 21 October 2013.
An investigation by the HSE found the ramp had not been securely attached to the trailer using both the chains it came with. Although one of the two chains had been attached, the other was left off as overhanging bushes made it difficult to get to the far side of the ramp.
The investigation also found the company had failed to risk assess the activity and monitor and enforce the safe system of work to ensure staff used all the safety critical features when attaching the ramp.
Linde Creighton Ltd, of Kingsclere Road, Basingstoke, was fined £8,000 and ordered to pay £1,144 in costs after pleading guilty to breaching Section 2(1) of the Health and Safety at Work etc Act 1974.
After the hearing, HSE inspector Caroline Lane said:
“Mr Jones had used the ramp at least twice a day to unload fork lift truck deliveries since the company bought it in 2008. The ramp manufacturer had provided instructions for its use, and safety warnings and precautions in the operating and maintenance manual clearly stated that unless restrained, the ramp could move away from the dock of the vehicle and that personnel could fall.
“The incident was therefore entirely foreseeable and preventable. Linde Creighton Ltd had a clear, easily achievable standard to meet but failed to achieve it, resulting in a painful injury to a member of staff.”
No comments:
Post a Comment